856: Reducing Errors and Optimizing Packing
As supply chains become increasingly complex and global, the importance of timely and accurate shipping information cannot be overstated. The 856 Advance Shipping Notice (ASN), significantly enhances supply chain management by providing detailed information about a shipment's contents, packaging, and expected delivery. This transparency not only prepares the recipient for the arrival of goods but also facilitates a smoother integration of these goods into inventory and sales systems.
This guide moves beyond the basics to provide best practices on optimizing the EDI 856 ASN for different packing methods and avoiding common 856 pitfalls. With a range of packing structures to consider, such as SOPI, SOTI, and SOTPI, tailoring the ASN to the specific needs of a shipment is key to leveraging its full potential.
Optimizing Packing Methods in EDI 856
By selecting the most appropriate packing structure for your shipments, you can ensure that the Advanced Shipping Notice you send is both comprehensive and tailored to the specific needs of your trade partners. Let’s delve into the various packing methods available and how they can be optimized in your EDI 856 documents.
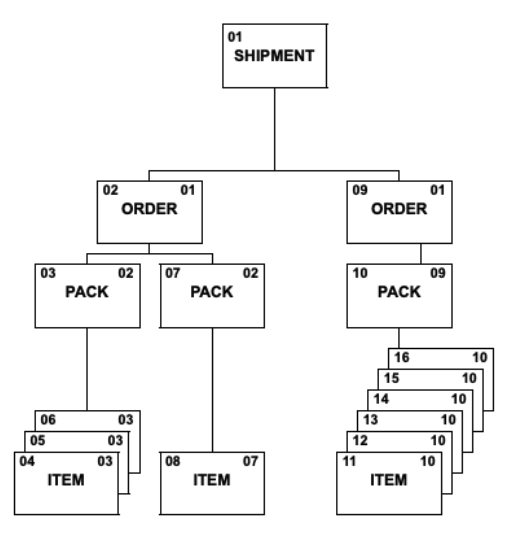
Pick and Pack Methods
SOPI (Shipment, Order, Pack, Item): This structure is ideal for shipments containing multiple orders, where each order includes various packs, and each pack contains multiple items. It's particularly beneficial for detailed tracking and management of items at every level of packaging, allowing recipients to prepare and plan for the incoming goods more effectively.
SOTI (Shipment, Order, Tare, Item): With a focus on the tare, or packaging materials, alongside the items, the SOTI structure is suitable for scenarios where the packaging itself is as important as the items being shipped. This might apply to shipments involving returnable containers or pallets, where tracking the return process is essential.
Currently unsupported "Pick and Pack" method for Web EDI:SOTPI (Shipment, Order, Tare, Pack, Item): Combining the detailed focus of SOPI and SOTI, the SOTPI structure is best for complex shipments where managing and tracking both the packaging materials and the individual items are critical. This comprehensive approach ensures nothing is overlooked, from the item level up to the overall shipment.
Standard Pack Methods
SOIP (Shipment, Order, Item, Pack): This structure simplifies the packing process for shipments containing homogenous cartons with many of a single item or SKU. By detailing the item level directly under the order, followed by the pack level, it streamlines the preparation of shipments with less variability in their contents.
Currently unsupported "Standard Pack" method for Web EDI:SOTP (Shipment, Order, Tare, Pack): Similar to SOTI but without detailing down to the item level within each pack, the SOTP structure is useful when the primary focus is on the packaging and the general contents of each order. This method is advantageous for shipments where item-level detail is unnecessary for the receiving process.
No Pack Level Details
SOI (Shipment, Order, Item): For shipments that don't require specific packaging details, the SOI structure focuses directly on the items within each order. This method is ideal for simpler shipments where the packaging process does not impact the receiving or inventory processes significantly.
By carefully considering these packing methods and applying them appropriately to your EDI 856 documents, you can achieve a higher level of precision and efficiency in your supply chain communications. The choice of packing structure should align with the complexity of the shipment, the requirements of the receiving party, and the specific needs of the items being shipped, ensuring that each Advanced Ship Notice you send out is perfectly suited to its purpose.
Avoiding Common EDI 856 Transmission Pitfalls
Navigating the complexities of EDI 856 transmissions requires an eye for detail and a proactive approach to avoid common pitfalls that can disrupt the flow of supply chain operations. Let’s explore these challenges and outline strategies for ensuring your Advanced Ship Notice submissions are accurate, timely, and complete.
Inaccurate Information
Incorrect quantities, wrong product codes, and mistakes in order details not only lead to inventory discrepancies and stocking issues but can also significantly impact sales and customer satisfaction. The solution lies in leveraging technology to mitigate human error. Orderful auto-maps item details from the original purchase order to the 856 document to drastically reduce discrepancies during shipping, ensuring that the information transmitted is as accurate and reliable as possible.
Timing Issues
The timing of ASN submissions is a delicate balance. Sending ASNs too late can cause delays in the receiving process, affecting inventory management and order fulfillment. Conversely, submissions that are too early, especially before the shipment is fully confirmed, can lead to confusion and inaccuracies if changes occur. Best practices for timing involve a rule of thumb: only send your 856 document when the shipment has been tendered to your transportation partner. This ensures that the information is final and reflective of the actual shipment, reducing the likelihood of timing-related issues.
Incomplete Documents
The completeness of an EDI 856 document is another critical factor in its effectiveness. Missing mandatory fields or providing insufficient product descriptions can hinder the receiving process, especially for complex shipments. The significance of Orderful validating the EDI 856 document against your trade partner's guidelines cannot be overstated. This validation process ensures that all necessary information is present and correct, facilitating a smooth transition from shipping to receiving.
Lack of Confirmation or Follow-Up
Finally, the importance of confirming the receipt of EDI 856 documents and promptly addressing any queries or concerns cannot be overlooked. Unresolved issues can lead to strained relationships and operational inefficiencies. Utilizing tools that monitor document acknowledgments, such as Orderful’s Transaction Status card, provides visibility into whether your trade partner has received and acknowledged the ASN. This level of oversight helps avoid communication breakdowns and ensures that any potential issues are addressed swiftly.
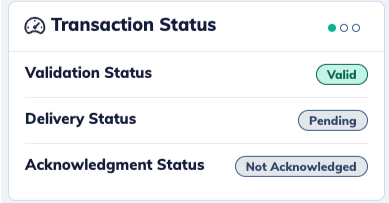
By being mindful of these common pitfalls and implementing strategic solutions, businesses can enhance the accuracy, timeliness, and completeness of their EDI 856 transmissions, leading to more efficient supply chain operations and stronger partnerships.
A Blueprint for Success: Your EDI 856 Guide
Tying it all together, let’s distill the essence of optimizing your EDI 856 submissions into a series of actionable steps that form the blueprint for success. From the importance of choosing the right packing methods to the crucial steps of validation and confirmation, the journey through EDI 856 best practices is about enhancing accuracy, ensuring timeliness, and fostering robust communication channels with your trade partners.
-
Precision Packing: Select the appropriate packing structure (SOPI, SOTI, SOTPI, etc.) tailored to the specifics of your shipment. This not only caters to the detailed requirements of your trading partners but also enhances the clarity and usability of the shipment information.
-
Auto-Mapping Accuracy: Leverage the capabilities of auto-mapping to ensure the transfer of details from the 850 purchase orders into your 856 documents is flawless. This reduces manual entry errors, ensuring the information relayed is as accurate as possible.
-
Timing is Everything: Perfect the timing of your ASN submissions to avoid the pitfalls of sending too early or too late. Aim for the sweet spot after the shipment has been tendered to the transportation partner, ensuring the information is both final and reflective of the actual shipment.
-
Detail-Oriented Documents: Validation against your trade partner's guidelines is non-negotiable. Ensure every required field is filled, and the descriptions are thorough, leaving no room for ambiguity or errors that could delay processing.
-
The Follow-Up Factor: Utilize tracking tools to confirm the receipt and acknowledgment of your ASNs. Prompt follow-up on queries and concerns not only smoothes out potential kinks but also reinforces the strength of your trade relationships.
Implementing the Best Practices
Embrace technology that supports these best practices, from auto-mapping to validation and tracking. But remember, technology is only as effective as the people using it. Educate your team, not just on the how-to’s but on the why’s, ensuring everyone understands the value and impact of optimized EDI 856 submissions.
Frequent reviews and updates to your processes will keep you aligned with the ever-evolving standards and expectations of your trade partners. Open communication lines for seamless collaboration and swift resolution of discrepancies underscore the essence of a well-oiled supply chain mechanism.
In essence, mastering your EDI 856 submissions is a blend of strategic planning, technological support, and dynamic collaboration. It’s about building a foundation that not only meets the current demands of your supply chain partners but is flexible enough to adapt to future changes, ensuring your operations remain at the pinnacle of efficiency and reliability.
Streamline Your EDI 856 with Orderful
Orderful simplifies the complexity of EDI 856 submissions, providing an intuitive platform that automates and validates your data against partner guidelines. With features like auto-mapping from 850 purchase orders to 856 documents and real-time tracking of document acknowledgments, Orderful ensures your Advanced Ship Notices are both accurate and timely. This not only minimizes errors but also strengthens your relationships with trading partners through reliable and transparent communication.
Ready to transform your EDI 856 submissions and elevate your supply chain efficiency? Speak to an expert at Orderful about your EDI management today.
Updated about 2 months ago